The Role of a Plastic Injection Molder in Modern Manufacturing
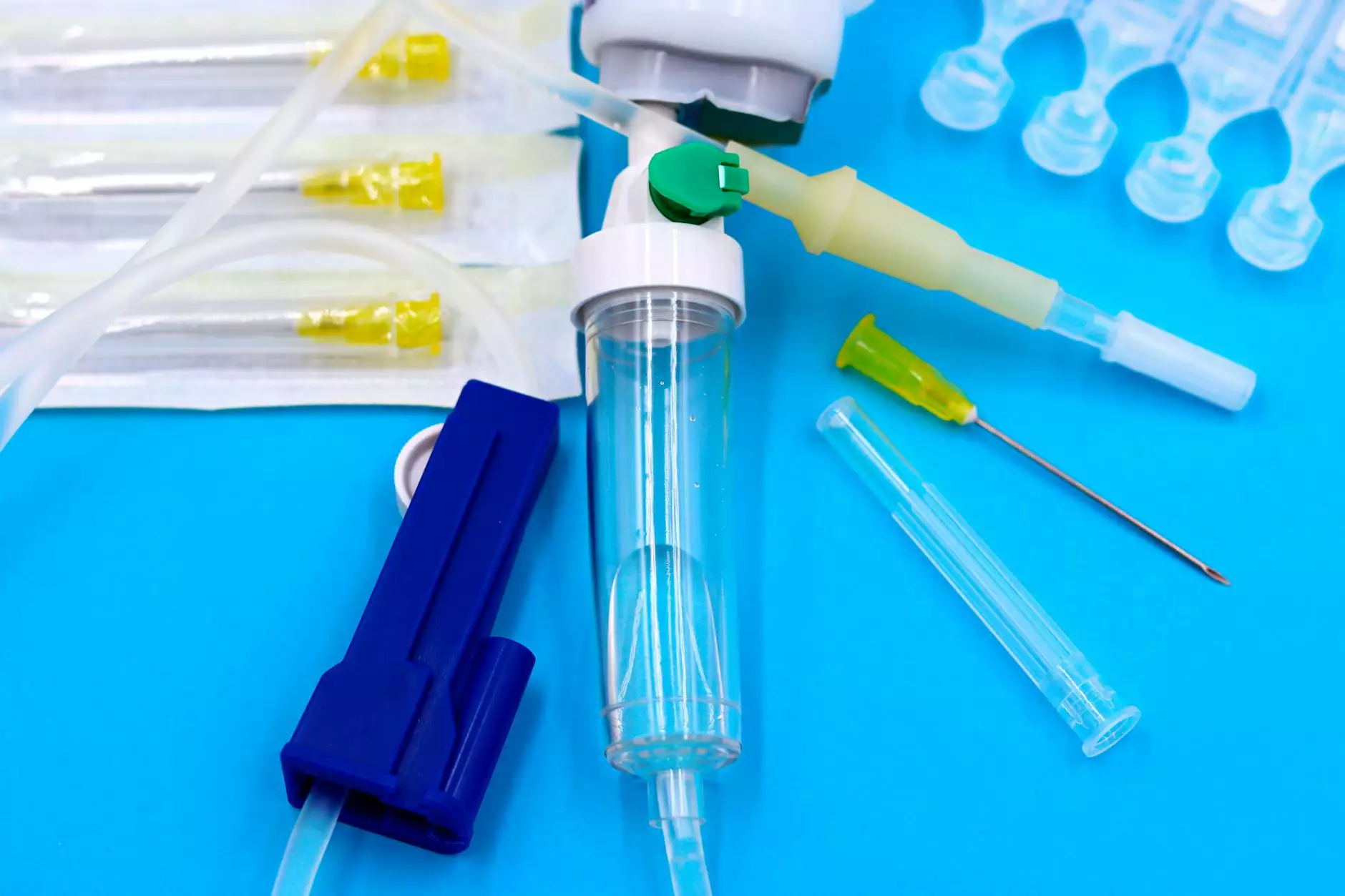
Introduction to Plastic Injection Molding
In today's competitive manufacturing landscape, efficiency, and precision are more critical than ever. Among the various techniques employed in manufacturing, plastic injection molding stands out as a highly effective method for producing a wide variety of parts and products. This process allows manufacturers to create intricate designs with high accuracy, making it an indispensable technique in various industries.
Understanding Plastic Injection Molding
Plastic injection molding is a manufacturing process that involves the injection of molten plastic into a pre-designed mold. Once the plastic cools and solidifies, it takes the shape of the mold, resulting in a finished product. This method is widely used due to its ability to produce complex shapes in a cost-effective and efficient manner. From automotive parts to consumer goods, the applications of this technology are virtually limitless.
The Injection Molding Process
- Material Selection: The process begins with selecting the appropriate thermoplastic material based on the product requirements and desired properties.
- Mold Design: A custom mold is designed, typically using computer-aided design (CAD) software to ensure precise specifications.
- Injection Phase: The plastic pellets are heated until they melt and are then injected into the mold under high pressure.
- Cooling Phase: Once the mold is filled, the plastic is allowed to cool, solidifying into the desired shape.
- Mold Removal: After cooling, the mold opens, and the finished product is ejected.
- Finishing Touches: The final step often involves secondary operations such as trimming, painting, or other surface treatments.
Benefits of Using a Plastic Injection Molder
Engaging the services of a reputable plastic injection molder offers numerous advantages for businesses looking to manufacture high-quality products.
1. High Efficiency and Speed
The plastic injection molding process is known for its speed. Once the mold is created, producing additional units is a quick and straightforward task. This efficiency is particularly beneficial for businesses that require large volumes of products or rapid production cycles.
2. Cost-Effectiveness
While the initial cost of mold creation can be substantial, the long-term savings associated with high-volume production make plastic injection molding a cost-effective solution. The ability to produce thousands of identical parts without significant additional costs can greatly enhance your profitability.
3. Design Flexibility
Plastic injection molding allows for a wide range of design possibilities. Complex geometries and intricate details can be achieved without significant additional costs. This flexibility encourages creativity in product design, enabling companies to innovate and differentiate themselves in the market.
4. Material Versatility
A variety of thermoplastics can be used in plastic injection molding, each offering different properties such as strength, flexibility, and resistance to chemicals. This versatility allows businesses to choose materials that best fit their specific applications. Additionally, innovations in biodegradable and recycled plastics are making this process even more sustainable.
5. Consistency and Quality Control
High-quality production is a hallmark of plastic injection molding. Automated processes contribute to production consistency, ensuring that each part meets strict quality standards. This reliability is crucial for industries such as automotive and medical, where component integrity is paramount.
Choosing the Right Plastic Injection Molder
Selecting the right plastic injection molder is critical to your project’s success. Here are several key considerations to keep in mind when making your choice:
1. Experience and Expertise
Look for a molder with a proven track record and extensive experience in the industry. An experienced plastic injection molder will better understand the nuances of different materials and injection techniques, allowing them to provide valuable insights throughout the production process.
2. Technology and Equipment
The technology and machinery used by a molder can significantly impact the quality and efficiency of production. Ensure that your chosen plastic injection molder invests in state-of-the-art equipment to increase productivity and maintain high standards.
3. Portfolio and References
Review the molder’s portfolio and ask for references from previous clients. A reliable plastic injection molder should be able to showcase a range of completed projects that highlight their capabilities.
4. Customer Service and Communication
Effective communication is key to a successful partnership. Choose a molder that prioritizes customer service and maintains open lines of communication throughout the project. This collaboration is essential for addressing any issues and ensuring that your project stays on track.
5. Cost Structure
While cost should not be the sole determining factor, it's important to understand the pricing structure of your potential plastic injection molder. Request detailed quotes and consider the long-term value of their services, rather than just the initial cost.
Applications of Plastic Injection Molding
The versatility of plastic injection molding enables its application across a wide range of industries. Here are some common areas where it plays a crucial role:
1. Automotive Industry
From interior components to exterior parts, the automotive industry relies heavily on plastic injection molding. This process allows for lightweight, durable parts that meet stringent safety and aesthetic standards.
2. Consumer Goods
Everyday products like toys, kitchenware, and electronic housings are often produced using plastic injection molding. The ability to produce large quantities quickly makes it ideal for meeting market demands.
3. Medical Devices
Medical devices require precision and reliability, making plastic injection molding an appropriate method for manufacturing components such as syringes, surgical instruments, and diagnostic equipment.
4. Packaging
The packaging industry benefits from plastic injection molding due to its ability to create lightweight, sturdy, and customizable packaging solutions that ensure product safety and appeal.
5. Electronics
Many electronic devices rely on custom plastic housings that are often created using plastic injection molding. The process allows for complex designs that house intricate circuits and components securely.
Future of Plastic Injection Molding
As technology continues to advance, the future of plastic injection molding looks promising. Innovations such as smart manufacturing, automation, and the integration of sustainable practices are shaping the industry. The use of CAD, 3D printing for mold prototyping, and the development of new composite materials are also paving the way for more efficient and environmentally friendly production methods.
Conclusion
In summary, plastic injection molding is a critical component of modern manufacturing. Its advantages in speed, cost-effectiveness, design flexibility, material versatility, and quality assurance make it the go-to method for producing high-quality plastic parts. Choosing the right plastic injection molder can significantly impact the success of your production, ensuring that your products meet the highest standards. As a key player in the manufacturing domain, considering the partnership with a competent and experienced molder is essential for sustained growth and innovation in today’s competitive market.
Contact Us
If you are looking for a trusted partner in plastic injection molding, look no further than deepmould.net. We specialize in providing high-quality molding services tailored to meet the specific needs of our clients. Contact us today to learn more about how we can help you achieve your manufacturing goals!