Comprehensive Guide to Tooling for Injection Molding
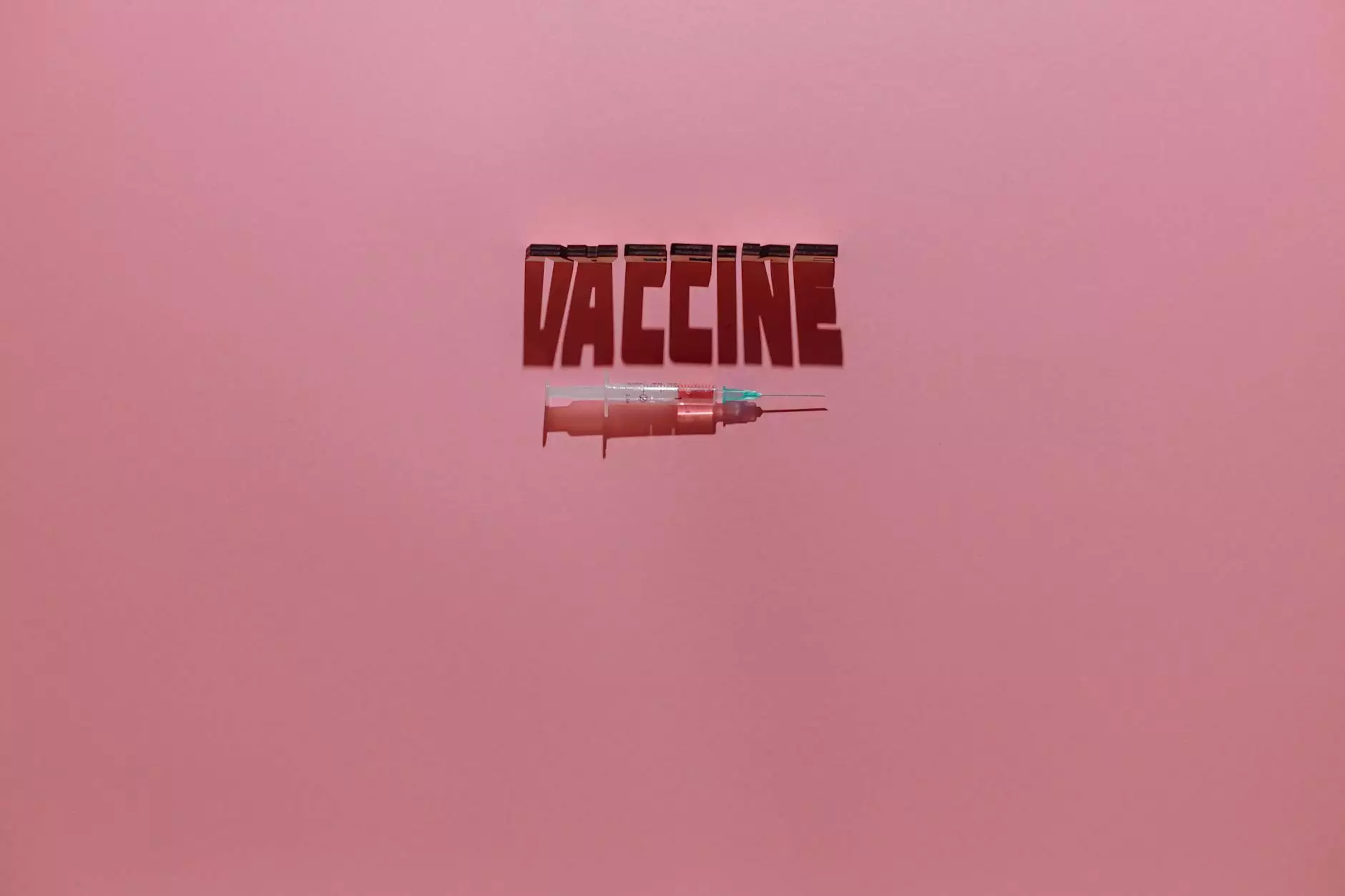
Tooling for injection molding is a crucial aspect of modern manufacturing processes, significantly influencing the efficiency and quality of production. This detailed article aims to explore the vital role of injection molding tooling, types, benefits, and the overall impact on businesses, particularly for metal fabricators like those represented by deepmould.net.
Understanding Injection Molding
Injection molding is a manufacturing process used for producing parts by injecting molten material into a mold. This process is most commonly associated with thermoplastics and thermosets. The tooling involved is a critical component, as it shapes the molten material into the desired final form.
What is Tooling?
Tooling refers to the creation of the various molds and dies that are used in the injection molding process. These tools are essential for defining the shape, size, and surface finish of the molded products. Quality tooling is necessary to ensure consistency, precision, and high production rates.
The Importance of Tooling in Injection Molding
- Precision Manufacturing: Tooling allows for precise shaping of materials, leading to high-quality end products.
- Cost-Effectiveness: Well-designed tooling can reduce material waste and lower production costs.
- Flexibility: Tooling can be adapted for various designs and product modifications, allowing manufacturers to fulfill diverse customer needs.
- Integration with Automation: Advanced tooling supports automation, enhancing productivity and efficiency.
Types of Tooling for Injection Molding
Tooling can be categorized into various types, depending on the material and design aspects:
1. Hard Tooling
Hard tooling involves the use of durable materials such as steel or aluminum to create molds. These tools have a longer lifespan and are ideal for high-volume production runs.
2. Soft Tooling
Soft tooling is made from less durable materials, like silicone or aluminum, and is used for lower volume production runs. It is faster and less expensive to produce, making it an excellent choice for prototypes or initial product testing.
3. Prototype Tooling
Prototype tooling is used to create initial samples or models of products. This type of tooling is often used in the early stages of product development to test designs and functionality.
4. Insert Molds
Insert molds allow for additional materials or components to be integrated into the molded product. This can enhance functionality or aesthetic appeal and is often seen in complex assemblies.
Benefits of Effective Tooling for Injection Molding
Investing in quality tooling is essential for businesses involved in injection molding. Here are some of the primary benefits:
1. Enhanced Product Quality
High-quality tooling leads to less variability, reducing defects in products. This consistency is critical for maintaining a solid reputation in the market.
2. Improved Production Efficiency
When the tooling is designed correctly, it allows for faster cycle times and reduced downtime during production. This efficiency translates into lower operational costs and increased profitability.
3. Cost Reduction
While the initial investment in tooling may seem substantial, high-quality molds can last longer and require less maintenance. Over time, this leads to significant cost savings.
4. Customization and Innovation
Investing in tooling enables manufacturers to innovate and offer customized solutions to meet specific customer demands. This ability to adapt quickly to trends can provide a competitive edge in the market.
Choosing the Right Tooling Material
Choosing the right material for tooling is vital. Most common materials include:
- Steel: Highly durable and ideal for high-volume production.
- Aluminum: Lighter and less costly, suitable for short runs or prototypes.
- Bronze: Often used for wear-resistant tooling due to its hardness.
Key Considerations When Designing Tooling
1. Product Complexity
More complex designs will require more sophisticated tooling solutions, often increasing manufacturing costs. Understanding the design's intricacy and how it will affect tooling is crucial.
2. Production Volume
Higher production volumes often justify the cost of hard tooling, whereas lower volumes may benefit from soft tooling, which can be produced more quickly and at a lower cost.
3. Material Selection
The choice of material for the final product will influence tooling design. Different materials may expand or contract differently, affecting the mold's design.
4. Cost-Benefit Analysis
Always perform a cost-benefit analysis when selecting tooling options. While cheaper tooling might save money upfront, it may lead to higher defects and additional costs down the line.
How to Maintain Injection Molding Tooling
Regular maintenance of tooling is critical to ensure its longevity and effectiveness. Here are a few best practices:
- Regular Inspections: Conduct frequent checks to identify wear and tear promptly.
- Proper Cleaning: Maintain a cleaning regimen to prevent material buildup that can affect product quality.
- Lubrication: Ensure that all moving parts are appropriately lubricated to reduce friction and wear.
- Storage: Store tooling in a climate-controlled environment to prevent damage from humidity or extreme temperatures.
Conclusion
In conclusion, tooling for injection molding is a fundamental element in the manufacturing landscape, particularly for metal fabricators striving to deliver high-quality, precise products. The design, material selection, and maintenance of tooling can significantly impact production efficiency, product quality, and ultimately, business success. By investing in effective tooling, businesses not only enhance their operational capabilities but also position themselves for innovation and growth in an increasingly competitive marketplace.
For those looking to enhance their injection molding processes, exploring the tooling solutions offered at deepmould.net can be a valuable step towards achieving excellence in manufacturing.