CNC Lathe Machine Parts Name: Essential Components for Precision Engineering
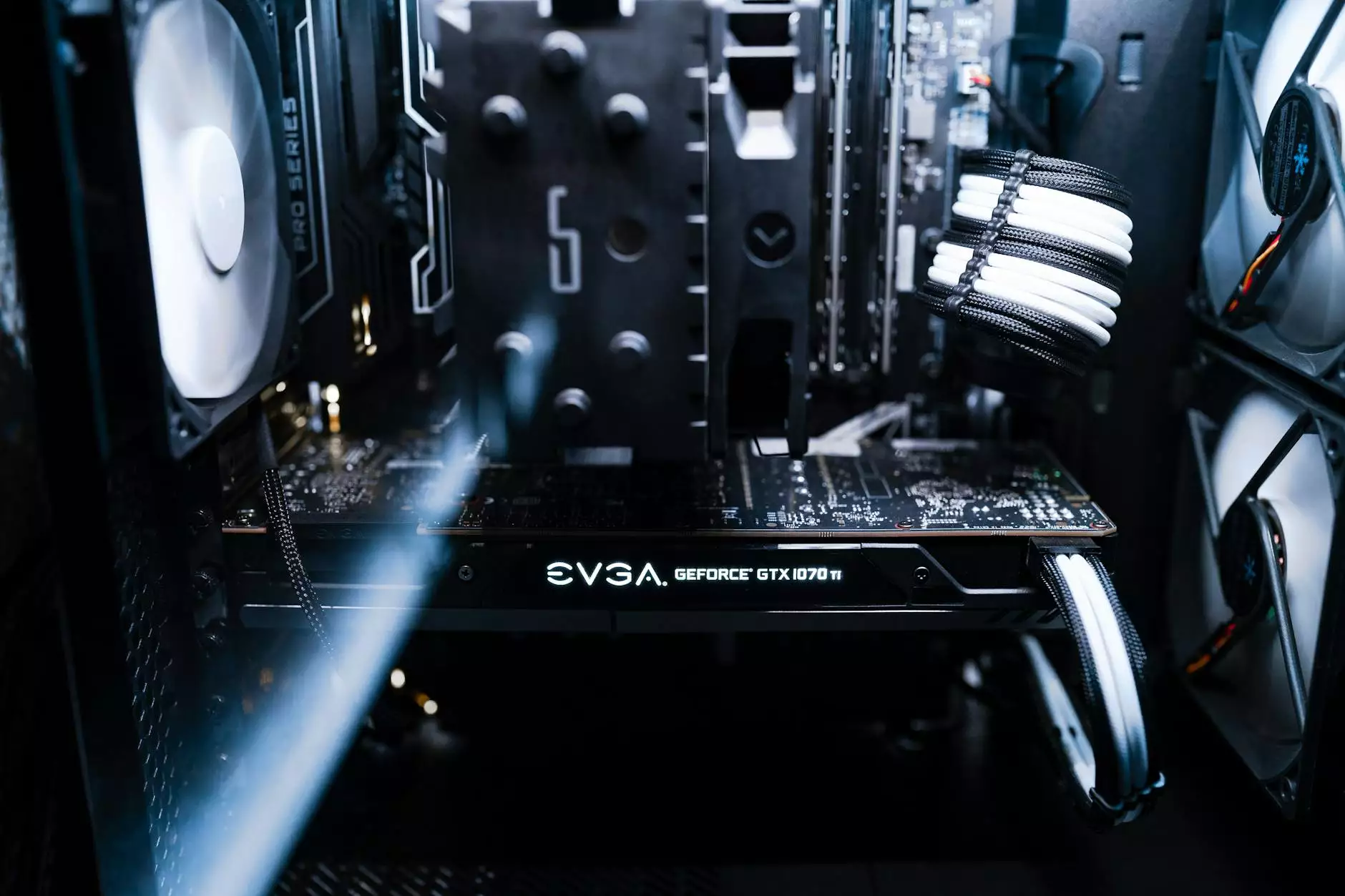
The world of metal fabrication is incredibly detailed and relies on precise machinery to create high-quality products. Amongst the various machines utilized in this field, the CNC lathe plays a pivotal role. Understanding the names of CNC lathe machine parts is crucial for those involved in manufacturing, engineering, and maintenance sectors. In this article, we will delve deep into the various components of a CNC lathe, their functions, and their significance in the metal fabrication industry. Through a comprehensive overview, you will gain valuable knowledge that can enhance both your expertise and operational efficiency.
What is a CNC Lathe?
aCNC lathe is a computer-controlled device used for cutting and shaping materials such as metal and plastic. Unlike traditional lathes that require significant manual input, CNC lathes operate using a computer program that controls the movements of the cutting tools based on precise measurements. This automation leads to greater accuracy, consistency, and efficiency in production.
Key CNC Lathe Components
Understanding a CNC lathe means familiarizing ourselves with its critical parts. Here’s an overview of essential cnc lathe machine parts names:
1. Bed
The bed is the main component of the CNC lathe, acting as the foundation for all other parts. It provides stability and rigidity to the machine, ensuring that operations can be performed with high accuracy.
2. Headstock
The headstock houses the spindle and motor. This part is responsible for rotating the workpiece, which is secured in place. The precision and power of the headstock greatly affect the machining speed and quality.
3. Tailstock
The tailstock complements the headstock and provides additional support to longer workpieces. It can be moved along the bed and often includes a quill for inserting tools or centers that help in drilling or boring operations.
4. Spindle
The spindle is the rotating part of the CNC lathe that holds the workpiece. Its design is critical because a high-strength spindle minimizes vibrations, improving the quality of the finished product.
5. Tool Holder
A tool holder secures the cutting tools in place during machining. The capability to quickly change tools enhances productivity, and there are various types, including turret and multi-station holders.
6. Carriage
The carriage is the part that moves the cutting tool along the length of the workpiece. It is responsible for the accurate positioning required for various cuts and shapes.
7. Cross Slide
The cross slide allows for the sideways movement of the cutting tool, enabling cuts to be made across the workpiece diameter. This part operates in coordination with the carriage to achieve intricate designs.
8. Leadscrew
The leadscrew translates the rotational motion of the motor into linear motion for the carriage. Its precision is vital for maintaining the exact movement needed for complex machining tasks.
9. Control Panel
The control panel is where the operator interfaces with the CNC lathe. It allows control over programming, speed adjustments, and tool changes, ensuring the machine runs according to the specified parameters.
10. Digital Readout (DRO)
The Digital Readout system provides real-time measurements of the position of the cutting tool. It enhances operational precision by enabling the operator to make exact adjustments during machining.
Importance of Each Part
Each component of a CNC lathe is designed to work together seamlessly to ensure precision and efficiency in manufacturing tasks. Here’s why these parts are indispensable:
- Precision: The meticulous design of each part contributes to the overall accuracy of machining processes.
- Efficiency: CNC technology allows for rapid production rates, which are enhanced by components like the tool holder and quick-change options.
- Durability: High-quality materials used in these components ensure that machines maintain performance over time, reducing wear and tear.
- Flexibility: Various attachments and tools can be used within the existing framework of a CNC lathe, making it adaptable for multiple operations.
Choosing the Right CNC Lathe for Your Business
When opting for a CNC lathe, several factors should be taken into consideration, including:
1. Size and Capacity
The dimensions of the lathe must meet your production needs. Consider both the maximum length and diameter it can accommodate.
2. Precision and Tolerance
Depending on the parts being manufactured, the precision level required might differ significantly. Ensure the machine can meet your tolerance specifications.
3. Control Software
Different CNC lathes come equipped with various types of control software. Choose one that aligns with your existing operations and has a user-friendly interface.
4. Support and Service
Reliable customer support and service options can minimize downtime. Research suppliers to find out about their service offerings and warranty plans.
Conclusion
In conclusion, understanding the cnc lathe machine parts names and their functions is integral for professionals working in metal fabrication. By knowing your equipment better, you can optimize operations, reduce maintenance costs, and enhance the quality of your final products. As the manufacturing industry continues to evolve, staying knowledgeable about the machinery you rely on can set you apart from the competition and position your business for success. If your business seeks to enhance its manufacturing capabilities, consider investing in high-quality CNC lathe machines from reputable suppliers like Deep Mould, known for their precision engineering and robust products.