Ultimate Guide to Die Casting Tooling
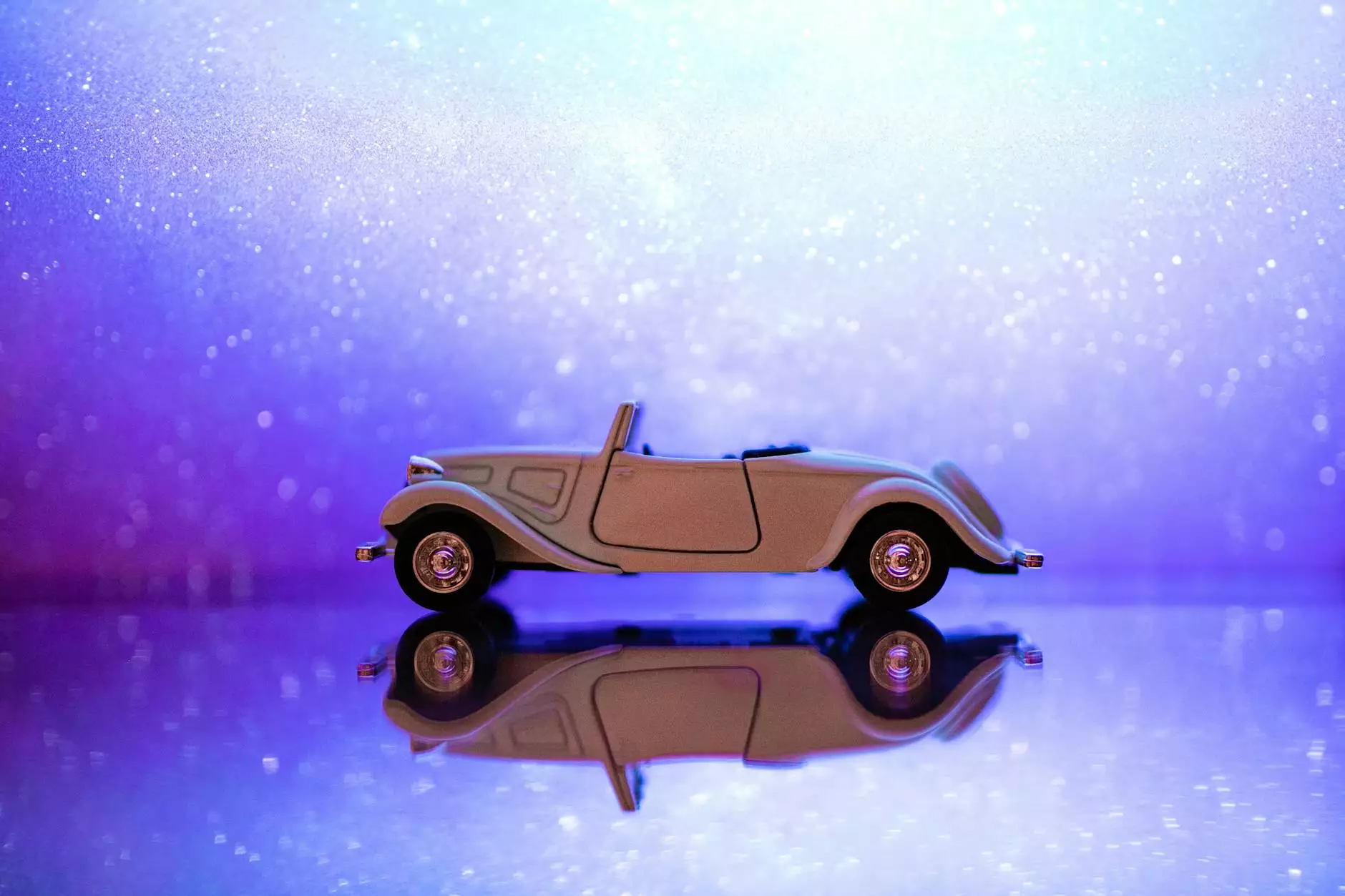
Understanding Die Casting Tooling
Die casting tooling is a critical component in the metal fabrication industry. It refers to the manufacturing process in which molten metal is injected into a mold cavity, allowing for complex shapes and high precision. This process is particularly prominent in producing parts where high-volume production is essential.
The die casting tooling itself comprises the molds, which are usually made from high-quality steel or aluminum, designed to withstand high temperatures and repeated cycles. At DeepMould.net, we specialize in providing top-tier die casting tooling solutions that cater to various industries.
Benefits of Die Casting Tooling
Die casting tooling presents numerous advantages:
- Precision and Accuracy: Components produced through die casting have exceptional tolerances, ensuring high dimensional accuracy.
- Complex Geometries: The process allows for the production of intricate designs that would be difficult or impossible to achieve with other manufacturing methods.
- Surface Finish: Die casting delivers a smooth surface finish, minimizing the need for additional machining and finishing processes.
- High Throughput: Once the tooling is made, mass production can occur rapidly, leading to cost savings in high-volume orders.
- Material Efficiency: The amount of scrap material generated during die casting is minimal, promoting greener manufacturing practices.
The Die Casting Tooling Process
The die casting tooling process consists of several key steps:
- Design: Initial designs are created using CAD software, which also assists in determining the tooling requirements.
- Tooling Development: Molds are crafted with precision, ensuring they align with the desired specifications.
- Melting: Metal alloys, commonly zinc, aluminum, magnesium, or copper, are melted to a suitable temperature.
- Injection: The molten metal is rapidly injected into the die under high pressure.
- Cooling and Ejection: Once the metal solidifies, the die is opened, and the finished part is ejected.
- Finishing: Additional surface treatments, if needed, can be carried out to achieve the final desired finish.
Material Selection for Die Casting Tooling
Choosing the right materials for die casting tooling is pivotal. The most commonly used materials include:
- Steel: Tool steels, such as H13, provide excellent durability and are ideal for high-volume production due to their longevity.
- Aluminum: Lightweight and resistant to corrosion, it is often used for tooling that does not require long production runs.
- Copper Alloys: Known for their excellent thermal conductivity and hardness, they are generally used in high-performance applications.
Challenges in Die Casting Tooling
While die casting tooling offers substantial benefits, it is not without its challenges:
- Tooling Costs: Initial investments in tooling can be high, making it less viable for low-volume projects.
- Maintenance: Regular maintenance is crucial to ensure that the tools are in optimal condition, which can add to operational costs.
- Material Limitations: Not all materials are suitable for die casting, which may restrict design possibilities.
Applications of Die Casting Tooling
Die casting tooling finds its applications across various industries, such as:
- Automotive: Components like engine blocks, transmission housings, and wheels.
- Electronics: Housings for electronic devices, connectors, and heat sinks.
- Aerospace: Structural components that require lightweight yet strength-heavy solutions.
- Consumer Goods: Everyday items ranging from appliances to decorative elements.
Innovations in Die Casting Tooling
The die casting industry is constantly evolving, incorporating new technologies and methods. Some noteworthy trends include:
- 3D Printing: Rapid prototyping techniques are being integrated to produce custom tooling faster and more efficiently.
- Smart Tooling: The integration of IoT technology in tooling to monitor temperature and pressure for optimizing production cycles.
- Recyclable Materials: Increased focus on using recyclable materials in the tooling process to enhance sustainability.
Why Choose DeepMould.net for Your Die Casting Tooling Needs?
At DeepMould.net, we pride ourselves on delivering unparalleled die casting tooling solutions tailored to meet the unique needs of each client. Here’s why we stand out:
- Expertise: Our team consists of highly skilled engineers and technicians with extensive experience in die casting tooling.
- Quality Assurance: We adhere to stringent quality control measures to ensure every tool meets industry standards.
- Customer-Centric Approach: We collaborate closely with clients to understand their needs, offering customized solutions that maximize efficiency.
- Advanced Technology: We utilize the latest technology and materials in our tooling processes, ensuring innovation and precision.
Conclusion
Die casting tooling is an indispensable aspect of modern manufacturing, providing reliable and efficient solutions across various industries. By choosing the right partner like DeepMould.net, businesses can leverage the full potential of die casting to enhance their production capabilities and achieve greater success. Whether you’re looking to develop new products or optimize existing processes, our expertise in die casting tooling is your gateway to achieving excellence in metal fabrication.
Contact us today to explore how we can support your die casting tooling needs and help you excel in your manufacturing endeavors!