The Unmatched Importance of a Concrete Mixing Plant
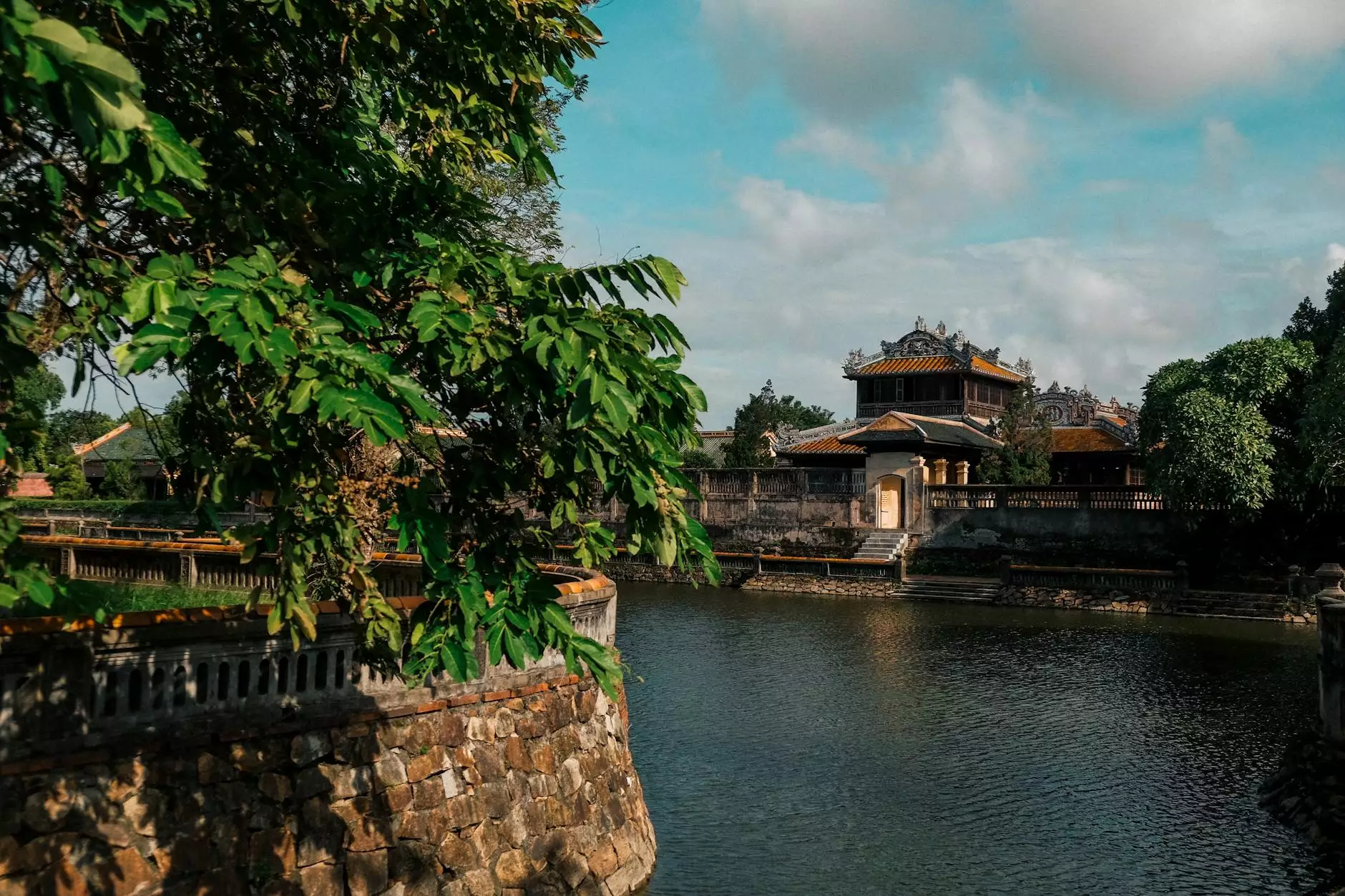
In the ever-evolving world of construction, efficiency and quality play a crucial role in determining the success of any building project. Among the primary factors that influence these parameters is the concrete mixing plant. This essential piece of equipment ensures that quality concrete is consistently produced, meeting both regulatory standards and project specifications. In this article, we will explore the various aspects of the concrete mixing plant, its operations, technological advancements, and its impact on the construction industry.
What is a Concrete Mixing Plant?
A concrete mixing plant is a facility designed to combine various components like gravel, sand, water, and cement to produce concrete of desired specifications. The plants come in various sizes and configurations, catering to different project demands.
Types of Concrete Mixing Plants
- Batch Mixing Plant: Concrete is produced in batches, allowing for precise control over the components mixed.
- Continuous Mixing Plant: This plant type produces concrete continuously, ideal for large-scale projects where volume is crucial.
- Mobile Concrete Mixing Plant: A portable option that can be relocated to various job sites, enhancing flexibility and operational efficiency.
- Central Mix Plant: Also known as a twin-shaft mixer plant, this type combines all materials before they are transported to the construction site.
Key Components of a Concrete Mixing Plant
Understanding the components of a concrete mixing plant is vital for anyone involved in the construction industry. Here are the major parts:
- Aggregate Bins: These store various aggregates in separate compartments, which helps in maintaining the quality of the concrete.
- Concrete Mixer: The heart of the plant, responsible for blending all materials uniformly.
- Cement Silo: This stores cement in bulk, ensuring a consistent supply and quality control.
- Water Meter: Accurately measures the amount of water to be added to the mix for achieving the desired consistency.
- Control System: Modern plants are equipped with sophisticated control systems, allowing operators to monitor and adjust production rates accurately.
The Production Process of a Concrete Mixing Plant
The production process in a concrete mixing plant is a vital point in ensuring the quality of concrete. The process typically involves the following steps:
1. Material Loading
Raw materials such as aggregates, cement, and additives are loaded into designated bins.
2. Batching
The next step is batching, where materials are weighed and recorded to ensure the right mix. Batch control systems ensure accuracy and efficiency.
3. Mixing
All components are then transferred to the concrete mixer, where they are blended to achieve a uniform consistency. This step is critical for the strength and durability of the final product.
4. Discharge
After mixing, the concrete is discharged into transporting vehicles or directly to the site, ensuring minimal delay.
Benefits of Using a Concrete Mixing Plant
The adoption of a concrete mixing plant brings numerous benefits to the construction industry:
- Quality Control: Provides consistent quality by precisely measuring and mixing materials.
- Time Efficiency: Speeds up the construction process by reducing the time taken from material aggregation to concrete delivery.
- Cost-Effectiveness: Reduces waste, ensuring that every batch produced adheres to project specifications.
- Environmental Benefits: Modern plants are designed to minimize emissions and recycle waste materials, contributing to sustainable practices.
The Role of Technology in Modern Concrete Mixing Plants
Technological innovations have transformed the landscape of concrete mixing plants. The integration of advanced software and hardware has revolutionized the entire production process. Here are some key technological advancements:
Automation
Automation has enhanced operational efficiency by reducing human error and improving accuracy. Automated control systems allow for real-time monitoring of all processes.
Telematics
Telematics systems enable remote monitoring and diagnostics, allowing operators to manage plants from a distance, ensuring continuous operation without manual intervention.
Energy Efficiency
Modern concrete mixing plants incorporate energy-efficient technologies, such as heat recovery and optimized mixing times, significantly reducing operational costs and environmental footprint.
Market Trends in Concrete Mixing Plants
The demand for concrete mixing plants is on an upward trajectory, driven by several market trends:
- Sustainability: There is an increasing focus on green construction practices, driving the demand for eco-friendly mixing solutions.
- Urbanization: Rapid urbanization and the growth of the infrastructure sector are fueling the need for advanced concrete production methods.
- Infrastructure Development: Governments across the globe are investing heavily in infrastructure projects, requiring reliable concrete mixing solutions.
Challenges Facing Concrete Mixing Plants
While the benefits are substantial, several challenges must be addressed to optimize the effectiveness of concrete mixing plants:
1. Raw Material Quality
Variability in raw material quality can adversely affect the final product. It's essential to establish strict quality control measures.
2. Equipment Maintenance
Regular maintenance of mixing equipment is crucial to prevent downtime and production delays, which can lead to financial losses.
3. Skilled Labor Shortage
The construction industry faces a shortage of skilled labor, impacting the operation of mixing plants. Training and development programs are necessary to address this issue.
The Future of Concrete Mixing Plants
As we look ahead, the future of concrete mixing plants is promising, driven by continuous advancements in technology and a focus on sustainable construction practices. Innovations such as:
- 3D Printing: The incorporation of 3D printing techniques in concrete production is anticipated to revolutionize the construction process.
- Smart Technologies: The rise of smart technologies and IoT integration will enhance monitoring and operational efficiency.
- Recycling Materials: Increased use of recycled materials in concrete production is likely to become the standard, promoting sustainability.
Conclusion
In conclusion, the concrete mixing plant is an essential component of modern construction, providing quality, efficiency, and cost-effectiveness. As the industry continues to evolve, embracing technological advancements and sustainable practices will ensure that concrete mixing plants remain at the forefront of high-quality concrete production. For businesses like Polygon Machinery, staying updated with these trends will not only enhance operational capabilities but also contribute to building a more sustainable future in construction.
Thus, investing in a state-of-the-art concrete mixing plant is not just a business decision but a step towards transforming how we build the world around us.